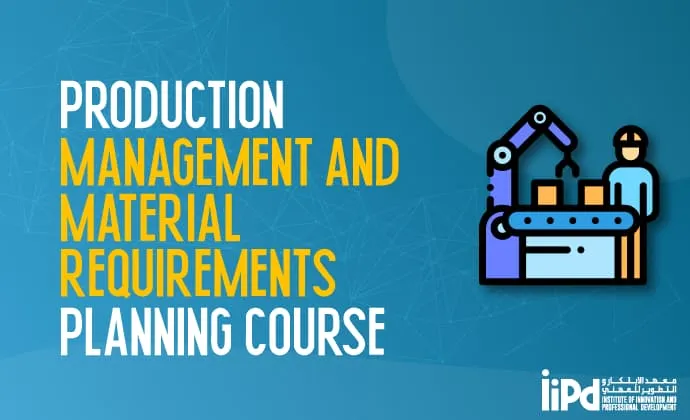
Course Details
In today's fast-paced business landscape, the efficient management of production and operations is crucial for the success of any organization. At IIPD Global, we recognize the significance of this facet of business and are committed to providing you with a comprehensive understanding of production and operations management.
In a dynamic business environment, accurate time estimates are invaluable. Our course delves into the concept of probabilistic time estimates, teaching you how to make reliable predictions in situations where outcomes are uncertain. This knowledge will assist you in realistic project planning and resource allocation.
Course Duration | 5 Days |
Course objective:
This course enables the participants to:
- Understand the definition of Planning and identify the types of Planning.
- Understand the different levels of operational planning
- Understand the relationship between planning and budgeting.
- Understand the concepts of integral quality management and benchmarking in their different aspects.
- Understand the strategic capacity management concept
- Understand the Sales and Operations Aggregate Planning process
- Understand the Material Requirements Planning method
Who should attend?
This course is concerned with the techniques to improve firms’ ways of production operation planning and how to use some instruments such as ratios and metrics to control it. Hence this course targets mostly managers, supervisors, and team leaders in all vocational operation areas within the organization.
Module "1" – Importance of Strategic Planning
- Operations Strategy
- Definitions and practical implications
- Levels of Strategy in Organizations
- Strategy alignment with Operations
- Investment in Manufacturing strategy
- Functional strategy
- Manufacturing Fundamental Concepts
- Tradeoffs
- Economies of Scale
- Differentiation
- Mixed strategy
- Postponement
- Standardization
- Economies of Scope
Module "2" Production Strategies and Configurations
- Product Classification
- Effect of Consumer Goods on Production
- Effect of Product Life Cycle on Production Planning
- Manufacturing Operations Strategies
- De-Coupling Point
- Production strategies decision making
- Push and Pull Planning systems
- MRP
- JIT
- Kanban
Module "3" Process Strategies and Configurations
- Production systems
- Continuous flow
- Discrete flow
- Process systems
- Intermittent
- Repetitive
- Continuous
- The Product-Process Matrix (PPM)
- Basic factory layouts
Module "4" Strategic Capacity Planning
- Importance of capacity planning decisions
- Determinants of effective capacity
- Key decisions in production capacity planning
- Tradeoffs between make or outsourcing
- Vertical and Horizontal integration
- Determining capacity bottlenecks and required investments
Module "5" Production Planning and Control of Resources
- Assembly Line Balancing
- Assembly Line Balancing Equations
- Ranked Positional Weight Heuristic
- Job Shop Scheduling
- Scheduling multi-tasks on One station
- Scheduling multi-tasks on Two stations
- Scheduling multi-tasks on Multi stations
Module "6" Production Planning methods and techniques
- Economical Production Quantity
- Identifying variables
- Building economical model
- Minimizing total cost
- MRPII (Manufacturing Resources Planning)
- The integrated functional model
- BOM (Bill of Material)
- Importance of Modular BOM and Super BOM
- RCCP (Rough Cut Capacity Planning)
- ERP vs MRPII and ERPII evolution
In an era where efficiency, precision, and adaptability define business success, mastering Production and Operations Management is more critical than ever. This course provides a robust foundation in strategic planning, production strategies, capacity management, and resource control—equipping participants with the tools and techniques needed to enhance operational performance and support long-term business goals.
Through a blend of theoretical concepts and practical applications, attendees will gain valuable insights into production systems, planning methodologies, and modern tools like MRP, JIT, and ERP. By understanding how to align operations strategy with organizational objectives, participants will be better prepared to make informed decisions, optimize processes, and drive continuous improvement across various operational domains.
Ideal for managers, supervisors, and team leaders, this course empowers professionals to contribute meaningfully to their organization’s operational excellence and strategic success.
Course Curriculum
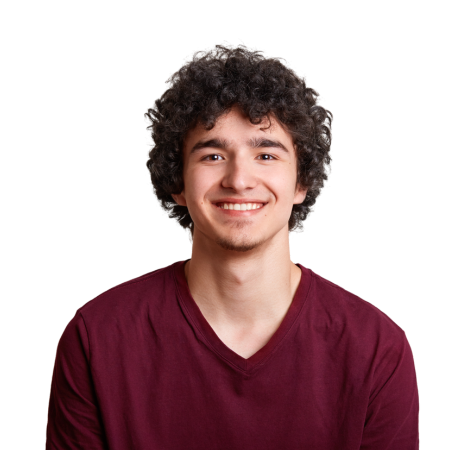
M.Ramzan
DeveloperI am a web developer with a vast array of knowledge in many different front end and back end languages, responsive frameworks, databases, and best code practices