In industrial automation, Programmable Logic Controllers (PLCs) play a pivotal role in controlling and monitoring various processes.
However, for these systems to function effectively, they rely on robust communication protocols that enable seamless data exchange between PLCs, sensors, actuators, and other industrial devices.
In this article, we will explore the different communication protocols employed in PLC systems, their use cases, popularity, and key facts.
1. DeviceNet
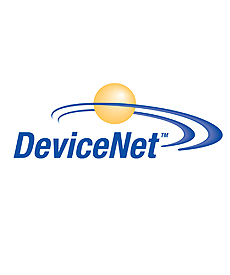
Developed by Allen-Bradley (now Rockwell Automation), DeviceNet is a widely adopted industrial network protocol based on the Controller Area Network (CAN) bus technology.
It is particularly suitable for connecting various devices in a single network, including sensors, actuators, and drives.
DeviceNet is known for its robustness, determinism, and ease of installation, making it a popular choice in various manufacturing environments.
2. Modbus
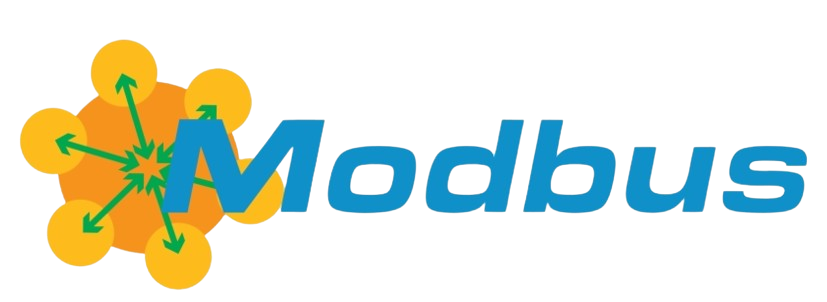
Modbus is one of the most widely used protocols in industrial automation, renowned for its simplicity and compatibility with a wide range of devices from different manufacturers. It operates over serial communication lines (Modbus RTU) or Ethernet networks (Modbus TCP/IP).
Modbus is particularly prevalent in applications such as building automation, energy management, and process control systems.
3. PROFIBUS
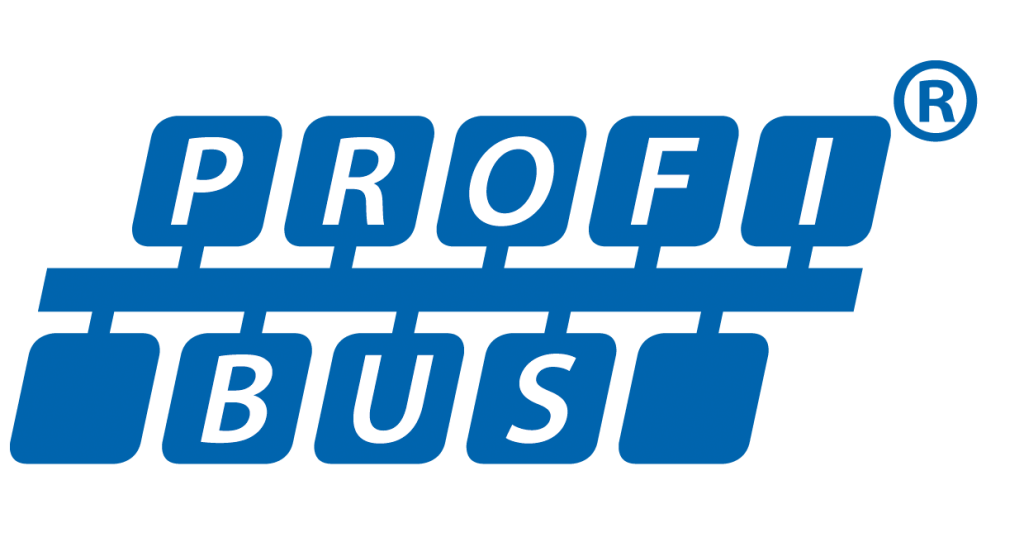
PROFIBUS (Process Field Bus) is a widely adopted field standard for industrial communication, developed by Siemens and other leading automation companies. It supports various profiles, including PROFIBUS DP (for decentralized peripherals) and PROFIBUS PA (for process automation). PROFIBUS is widely used in industries such as automotive, food and beverage, and chemical processing.
4. DF1 protocol
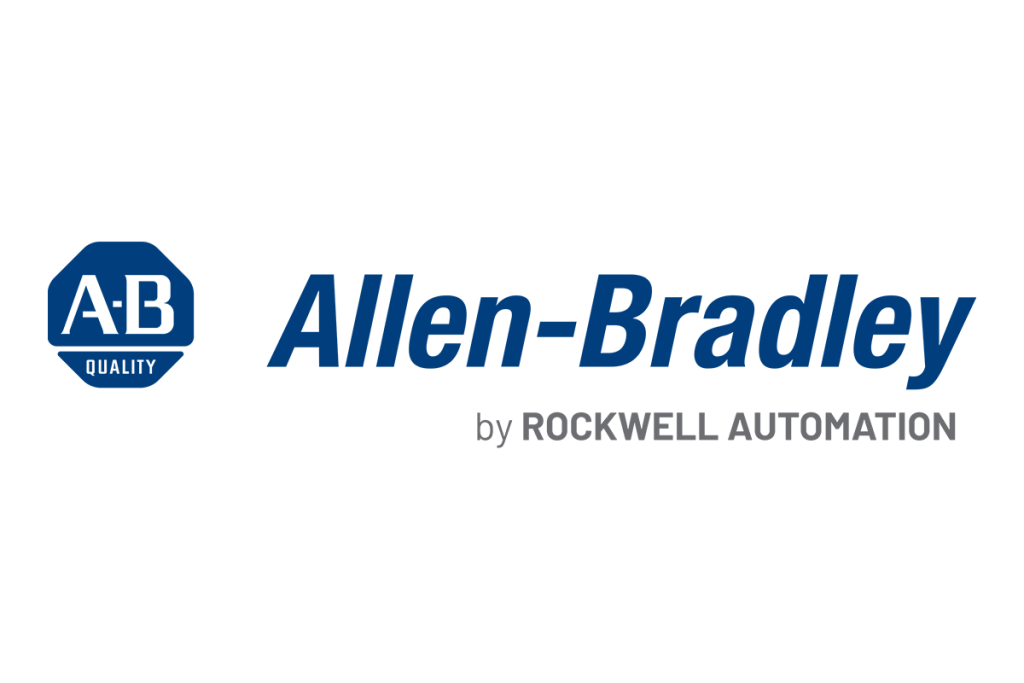
The DF1 protocol, also known as the Allen-Bradley Data Highway protocol, is a proprietary communication protocol developed by Rockwell Automation for exchanging data between PLCs and other devices. It is commonly used in Allen-Bradley PLCs and is known for its simplicity and efficiency in small to medium-sized applications.
5. EtherCAT
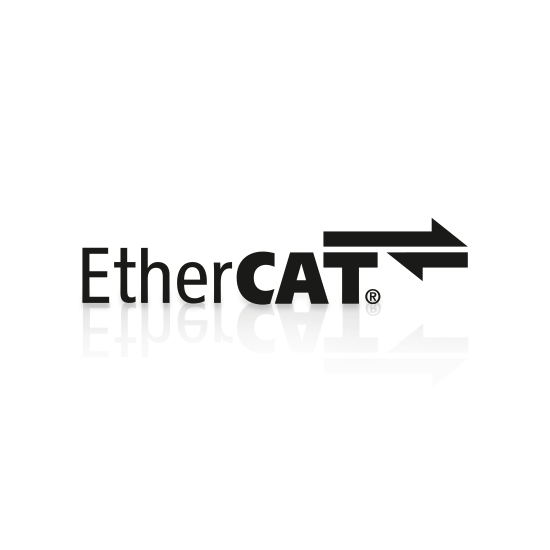
EtherCAT (Ethernet for Control Automation Technology) is a real-time Ethernet protocol designed for high-performance motion control and automation applications. It offers fast data transfer rates, low communication jitter, and precise synchronization, making it suitable for applications that require high-speed control and determinism, such as robotics and semiconductor manufacturing.
6. ControlNet
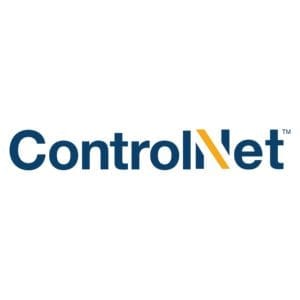
ControlNet is a real-time communication protocol developed by Rockwell Automation for industrial automation applications. It is based on the CTDMA (Concurrent Time Domain Multiple Access) technology and is designed for high-speed data transfer and deterministic control. ControlNet is often used in applications that require tight integration between various devices, such as motion control systems and process control systems.
7. HART protocol
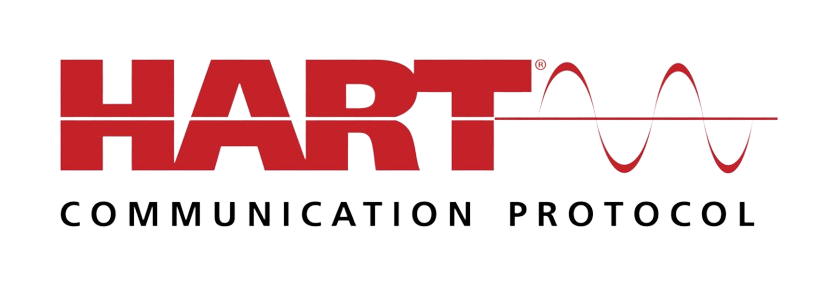
The HART (Highway Addressable Remote Transducer) protocol is widely used in process control applications for communication between intelligent field devices, such as transmitters and actuators, and control systems. It operates over traditional 4-20 mA analog wiring, allowing for digital communication and remote configuration of field devices without disrupting existing infrastructure.
8. PROFINET
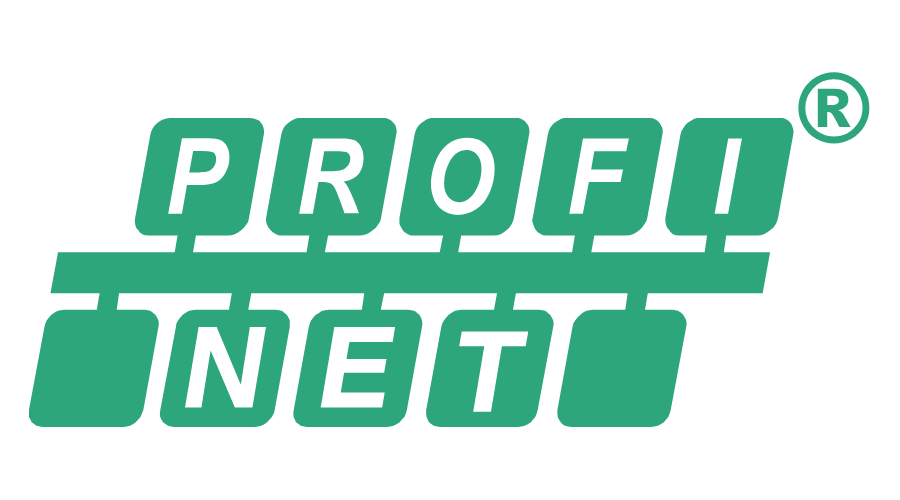
PROFINET (Process Field Network) is an industrial Ethernet standard developed by Siemens and other leading automation companies. It is designed for real-time communication in automation systems and supports various profiles, including PROFINET IO (for input/output devices) and PROFINET CBA (for component-based automation). PROFINET is widely adopted in various industries, including automotive, food and beverage, and discrete manufacturing.
9. Fieldbus
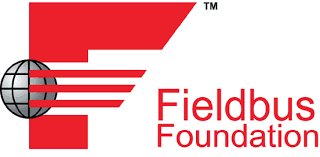
Fieldbus is a general term referring to various industrial communication protocols used for connecting field devices, such as sensors and actuators, with control systems. Examples of Fieldbus protocols include FOUNDATION Fieldbus, PROFIBUS, and HART, each with its characteristics and applications in different industrial sectors.
10. CANopen
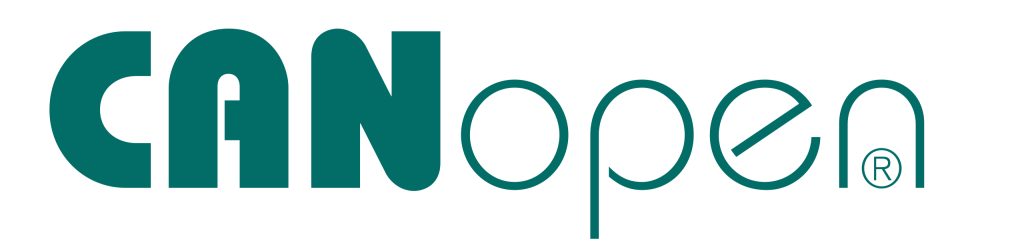
CANopen is a higher-level protocol built on top of the Controller Area Network (CAN) bus technology. It is designed for motion control and industrial automation applications, providing a standardized communication framework for connecting various devices, such as drives, sensors, and actuators. CANopen is known for its flexibility, robustness, and ease of integration.
11. CAN bus
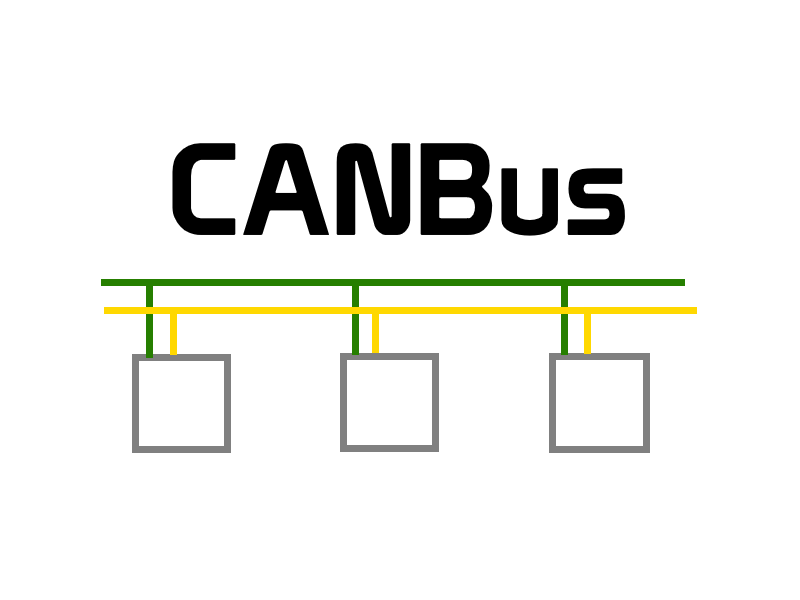
The Controller Area Network (CAN) bus is a robust and reliable communication protocol widely used in automotive and industrial applications. It is designed for real-time communication between various devices, such as PLCs, sensors, and actuators, and is known for its error-handling capabilities and resistance to electrical interference.
12. DNP3
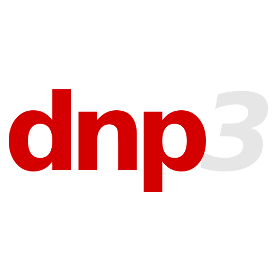
The Distributed Network Protocol (DNP3) is an open and interoperable communication protocol commonly used in the electric utility and process control industries. It is designed for communication between master stations (such as SCADA systems) and remote terminal units (RTUs) or intelligent electronic devices (IEDs), enabling reliable data exchange and control over various communication media.
Conclusion
In the ever-evolving landscape of industrial automation, the selection of the appropriate communication protocol plays a crucial role in ensuring efficient and reliable data exchange between PLCs, sensors, actuators, and other industrial devices.
Each protocol has its unique strengths and is tailored to specific application requirements, such as real-time performance, determinism, fault tolerance, and ease of integration. By understanding the nuances of these protocols, industrial automation professionals can make informed decisions and implement robust systems that drive productivity, efficiency, and overall operational excellence.
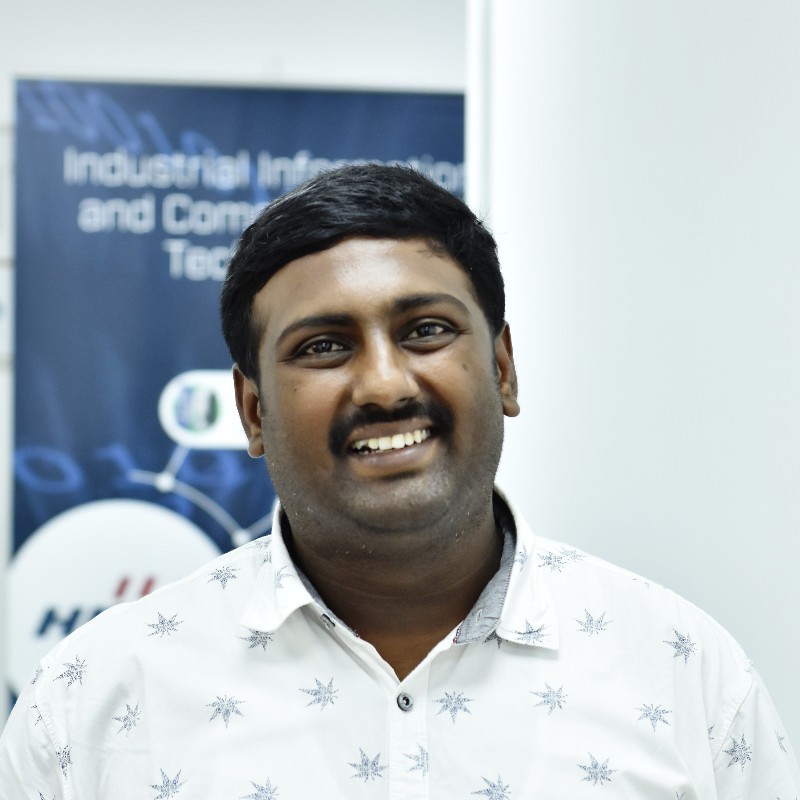
Senior Tech Manager at IIPD Global, weaving magic in Industrial, Building, and home Automation. KNX Tutor on a mission! Embracing Industry 4.0 and proudly shaping the tech landscape. Certified by CertNexus to ignite minds!