As an automation expert, understanding the intricacies of PLC power supplies is crucial for ensuring system reliability and efficiency. Programmable Logic Controllers (PLCs) are the backbone of industrial automation, and their power supplies play a pivotal role in maintaining uninterrupted operations. This comprehensive guide delves into the essential aspects of PLC power supplies, including voltage requirements, handling voltage variations, and selecting the right power supply for your system.
Components of a PLC System
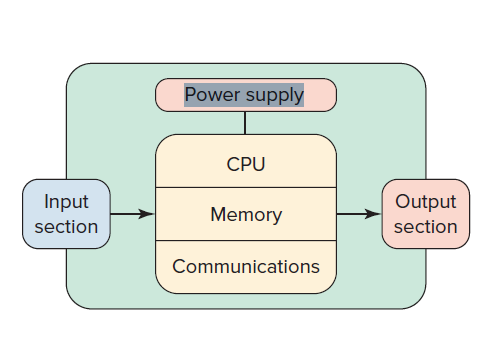
A typical PLC system is divided into several key components:
- Central Processing Unit (CPU): The brain of the PLC, responsible for processing and executing control instructions.
- Input/Output (I/O) Section: Interfaces with field devices to receive inputs and send outputs.
- Power Supply: Provides the necessary DC power to the CPU and I/O modules.
- Programming Device: Used to program and configure the PLC according to the application’s requirements.
The power supply is essential as it supplies DC power to other modules plugged into the rack. In large PLC systems, this power supply typically does not power field devices; instead, external AC or DC supplies are used. However, the power supply may also power field devices in smaller micro-PLC systems.
Voltage Requirements
Voltage requirements for PLC systems typically involve either AC or DC power, with common operating voltages being 24V DC, 120V AC, or 240V AC. Ensuring the power supply matches these requirements is crucial for stable and reliable PLC operation, preventing malfunctions and potential damage.
AC vs. DC Power
PLCs can operate on AC or DC power, with common voltages being 24V DC, 120V AC, or 240V AC. It’s imperative to ensure that the power supply matches the PLC’s voltage requirements to prevent malfunctions or damage.
Stability is Key
PLCs require a stable power supply. Voltage fluctuations or spikes can cause malfunctions, system shutdowns, or even damage to PLC components. Therefore, a power supply that can handle line fluctuations within the PLC’s operating range is essential.
Power Supplies for Different PLC Systems
Power supplies for different PLC systems vary depending on the system’s voltage and power needs. Larger PLC systems typically use external power supplies for field devices, while smaller micro-PLC systems may use an internal power supply to power both the CPU and field devices, ensuring efficient operation tailored to the system’s size and requirements.
PLCs Operating at 230V AC
PLCs designed to work with 230V AC can be directly connected through a fuse or a Miniature Circuit Breaker (MCB) to a single-phase AC source. The line voltage is:
- Stepped Down using a transformer.
- Rectified to convert AC to DC.
- Filtered with capacitors to smooth out the voltage.
- Protected throughout the process to prevent damage.
All these components are integrated into a compact power supply unit.
PLCs Requiring 24V DC
For PLCs that require 24V DC, a Switched Mode Power Supply (SMPS) is used to convert 230V AC to 24V DC. SMPS units are efficient and provide the necessary DC voltage with minimal ripple and noise.
Power Supply for I/O Modules
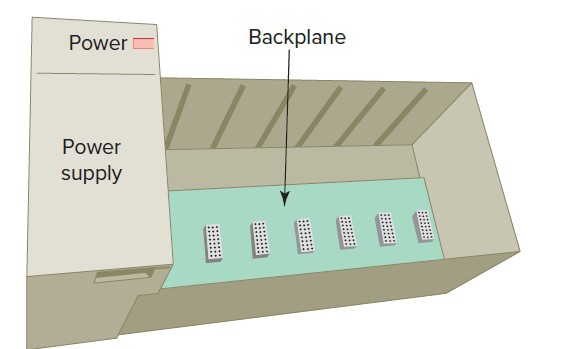
The PLC power supply provides power not only to the processor but also to the I/O modules plugged into the backplane of the rack. Key points include:
- Backplane Power: Powers the electronics on the I/O module circuit boards.
- User-Supplied Power: Higher currents required by output modules are typically provided by external power sources.
- Module Ratings: Power supplies may be rated for 3 A, 4 A, 12 A, or 16 A, depending on module types and quantities.
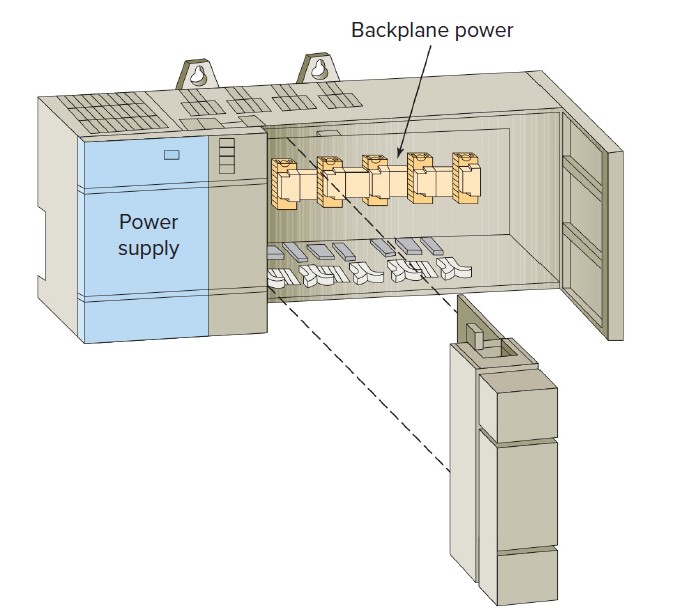
External Power Supplies
Some modules require an external power supply. In such cases:
- Choose an SMPS or transformer with higher current and load ratings.
- Ensure it can power the CPU, modules, and other panel components effectively.
- Match the power supply specifications with the requirements of all connected devices.
Handling Voltage Variations and Surges
Handling voltage variations and surges is crucial to maintaining the stable operation of a PLC system. Power supplies are designed to tolerate minor fluctuations, but excessive voltage spikes or dips can lead to system shutdowns. To prevent this, constant voltage transformers and isolation transformers are often used to shield the PLC from disturbances, ensuring uninterrupted performance even in environments with unstable power conditions.
Built-In Tolerance
PLC power supplies are designed to:
- Sustain Line Fluctuations: Maintain operation within specified voltage ranges.
- Withstand Momentary Losses: Typical hold-up times range from 10 milliseconds to 3 seconds.
Preventing Shutdowns
- System Shutdowns: Occur when voltage fluctuations exceed acceptable ranges.
- Solutions:
- Install a Constant Voltage (CV) Transformer to minimize shutdowns due to voltage variations.
- Use Isolation Transformers to shield the PLC from electrical disturbances caused by other equipment.
Best Practices
- Place the PLC power supply and I/O devices on a separate transformer.
- This transformer can also be a step-down transformer to reduce incoming voltage to desired levels.
Auxiliary Power Supplies
An auxiliary power supply is not associated with the processor but is crucial for:
- Supplying logic power to remote I/O racks.
- Supporting other processor-related hardware.
- Often referred to as remote power supplies.
Selecting the Right Power Supply for Your PLC
When choosing a power supply, consider the following parameters:
- Rated Voltage: The voltage output that the power supply is designed to deliver.
- Rated Current: The maximum current the power supply can provide without overheating.
- Rated Power: The total power output capacity, typically expressed in watts.
- Ripple and Noise: Unwanted residual periodic variations in the DC voltage.
- Voltage Adjustable Range: The extent to which the output voltage can be adjusted.
- Voltage Tolerance: The allowable deviation from the specified output voltage.
- Line Regulation: Ability to maintain constant output despite changes in input voltage.
- Load Regulation: Ability to maintain constant output voltage despite changes in load current.
Conclusion
The appropriate power supply for your PLC is vital for system performance and longevity. By understanding voltage requirements, preparing for voltage variations, and carefully evaluating power supply specifications, you ensure that your PLC system operates reliably and efficiently.
Optimize your automation systems by giving due attention to the power supply—it’s the lifeline of your PLC. With the right knowledge and equipment, you can safeguard your operations against unexpected downtimes and enhance overall productivity.
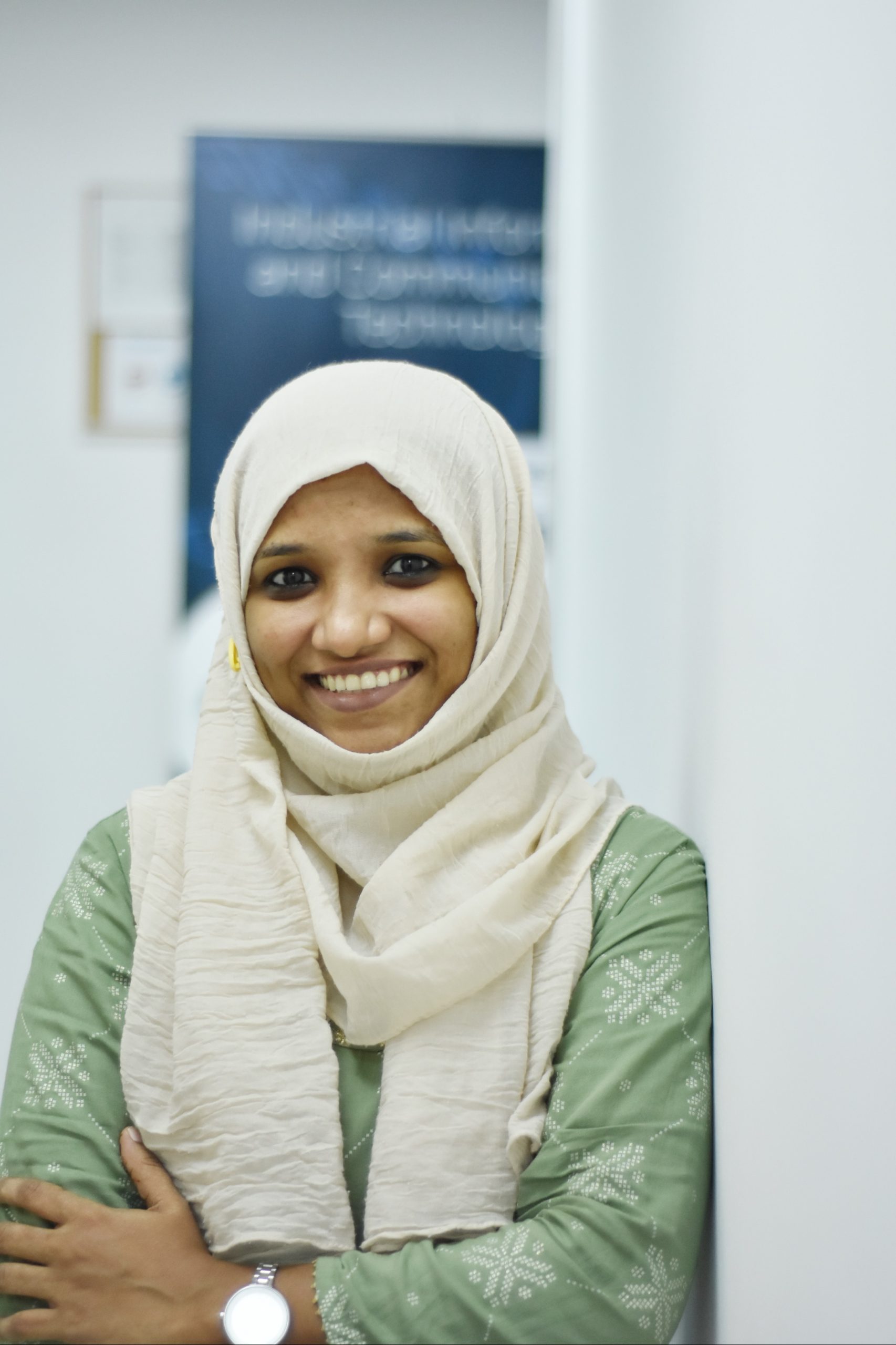
Fathima Sadina works as a Technical Associate at IIPD, where she dives into the world of Industrial Automation, focusing on PLC, SCADA, and VFD systems. With a keen passion for spreading know-how, she loves to craft engaging blog posts on a wide array of technical subjects.