In the evolution of industrial science, simulation, and emulation has become vital for virtual commissioning processes. Testing of real-world automation systems could be done virtually, mimicking a real automation system. This project documents current thinking on creating simulation and emulation models to provide feedback to industrial PLC programs to test their logical operation before commissioning.
Both approaches are trying to create the same output as in a real-world automation system. Still, with emulation, testing of PLC programs goes a step further by minimizing the gap between reality and the virtual world.
The simulation can be used in a demonstration of a real industrial process functionality and for testing the control algorithm on interactive realistic models of machine tools in the VR environment, while the real programmable logic controller controls the industrial process.
VIRTUAL CONTROL
VC projects are performed to verify PLC programs in a simulation environment before the physical implementation for which all resources are modeled virtually without any risk of endangering lives and equipment. Testing of PLC programs can provide decision-making support for different engineering fields and real-time communication between PLC and the simulation model.
A VC project involves three distinct factors:
- Mechatronic design including actuators, sensors, and functional descriptions.
- Machine control including inputs and output signals.
- Connection between sensors, actuators, and the control program.
PLC Simulators
PLC (Programmable Logic Controller) simulation and virtualization tools are essential for testing, developing, and simulating industrial automation processes without the need for physical PLC hardware. Here are some popular tools used in the industry:
RSLogix Emulator:
This is a software emulator for the Allen-Bradley line of PLCs, allowing you to test and debug ladder logic programs without physical hardware.
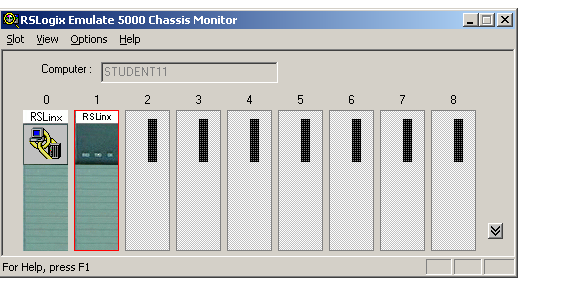
RSLogix 5000 Emulator software acts as a PLC CPU, it does not have any input/output modules. In most cases, this is sufficient to test the code and make sure the SCADA clients can receive/send data from/to PLC.
Siemens PLCSim:
Simulates the S7-1500, S7-1200, and other Siemens PLCs. It integrates with the TIA Portal (Totally Integrated Automation) for comprehensive simulation and testing.
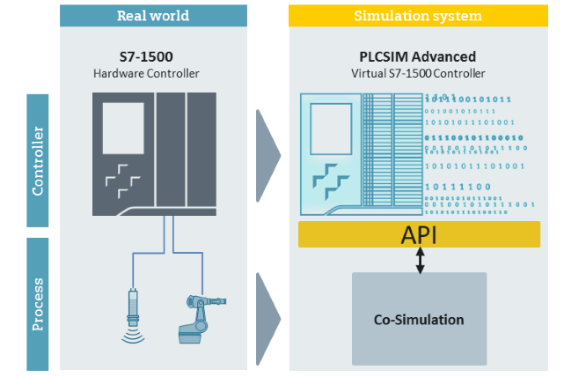
With the SIMATIC S7PLCSIM Advanced virtual controllers for the simulation of a S7-1500 or ET 200SP CPU are created and used for the comprehensive simulation of functions. Therefore no real controllers are required to test a STEP 7 program.
The virtual controllers can also be tested in the context of a system or machine. The user interface (API) is used to connect the virtual controller to a system or machine simulation (co-simulation). A STEP 7 program created in STEP 7 V14 controls a conveyor system.
For a comprehensive function test, the STEP 7 program is loaded via S7-PLCSIM Advanced into a virtual S7-1500 controller. This controller interacts via the API with a co-simulation (plant simulation), to validate the STEP 7 program in the context of the plant.
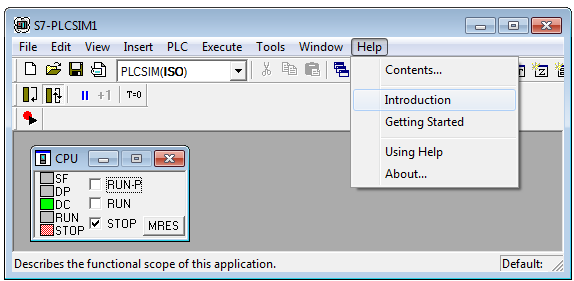
Virtual PLC Software
Virtual PLC software offers a digital platform for designing, simulating, and testing PLC programs without the need for physical hardware. This powerful tool enables engineers and students to develop and refine automation solutions efficiently, reducing costs and minimizing risks associated with physical prototyping.
By providing a virtual environment to experiment with different PLC configurations and logic, users can accelerate the development process, enhance troubleshooting capabilities, and gain a deeper understanding of PLC operation. In the following sections, we will explore a variety of virtual PLC software options available in the market
TwinCAT (Beckhoff)
Offers a complete virtualization environment for Beckhoff PLCs. It supports real-time simulation and can be used for both PLC and PC-based control systems. It supports the creation of a virtual machine, which corresponds to a real one in its runtime performance.
The task of the TwinCAT Simulation Manager is essentially to break and restore links, such as between a PLC variable and an IO point. In the case of simulation, the link is broken and reconnected to a simulation environment.
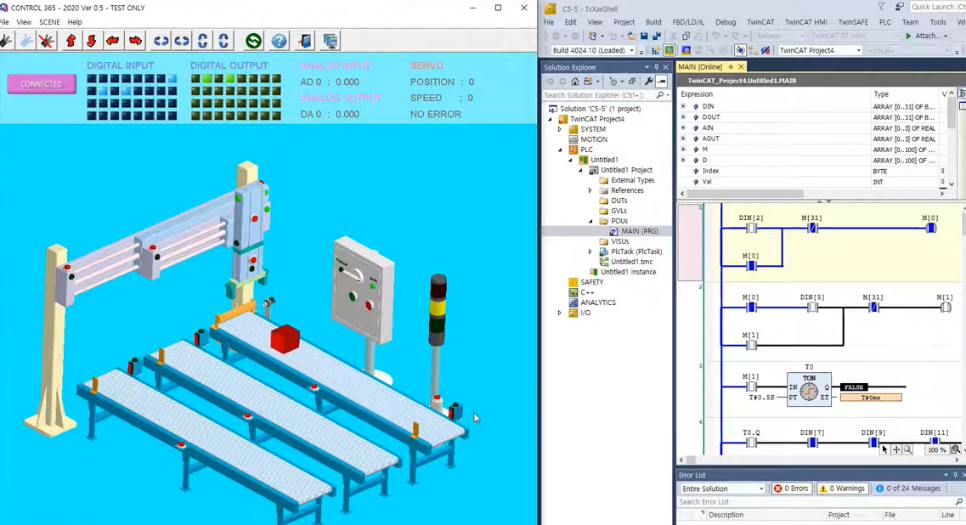
Codesys Virtual PLC
Allows you to simulate PLC programs created with the Codesys development environment. It supports various PLC hardware configurations and protocols.
CODESYS Virtual Control has no hardware requirements.CODESYS provides hardware-independent Soft PLCs with and without real-time for Windows, as well as Soft PLC solutions for Linux x86 and ARM-based systems
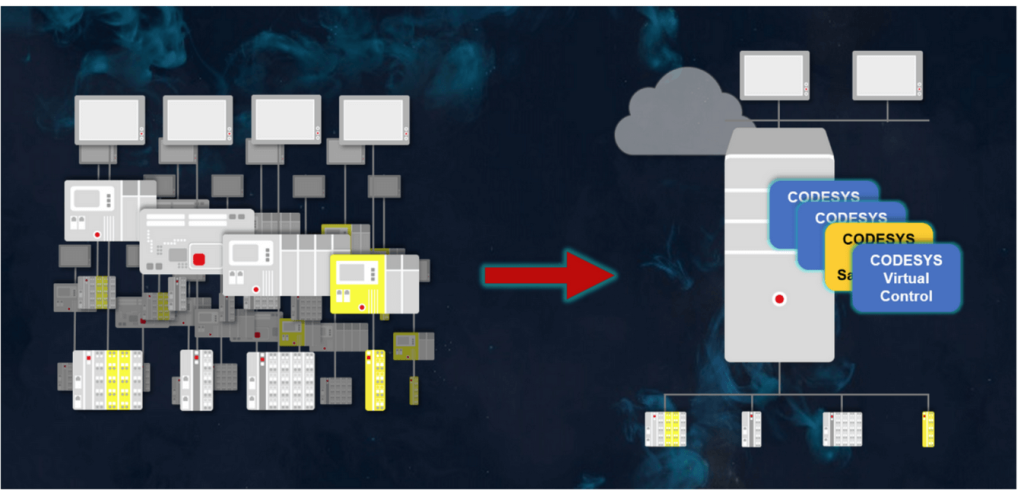
MATLAB/Simulink
Provides simulation capabilities for control systems, including PLCs, with extensive support for modeling and simulation of industrial processes.
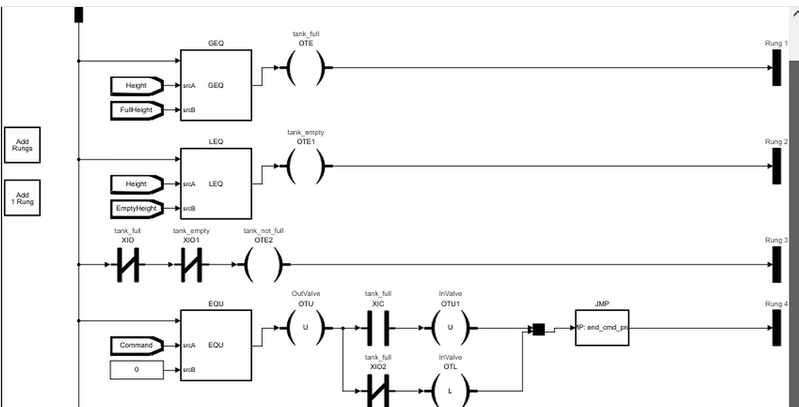
Simulink PLC Coder generates hardware-independent IEC 61131-3 Structured Text and Ladder Diagrams from Simulink models, Stateflow charts, and MATLAB functions.
Structured Text is generated in PLCopen XML and other file formats supported by widely used integrated development environments (IDEs), including 3S-Smart Software Solutions CODESYS®, Rockwell Automation Studio 5000, Siemens TIA Portal, and Omron® Sysmac® Studio.
Ladder diagrams are generated in file formats supported by Rockwell Automation Studio 5000. As a result, you can compile and deploy your application to numerous programmable logic controller (PLC) and programmable automation controller (PAC) devices.
https://www.mathworks.com/products/simulink-plc-coder.html/
Automation Studio (B&R)
Offers simulation tools for PLC programming, motion control, and HMI development. It supports the virtual commissioning of automation systems.
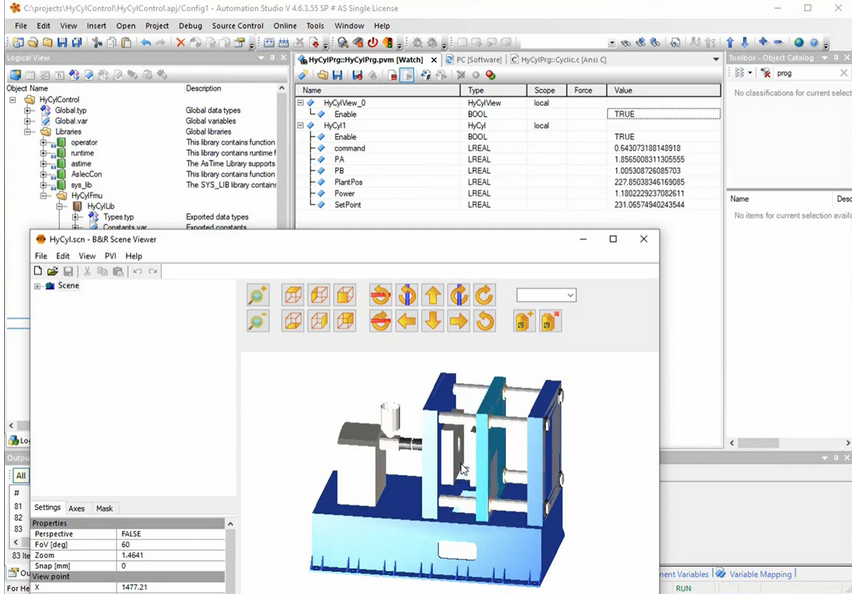
List of Generic PLC Simulation Tools
- Festo FluidSIM:
Simulates pneumatic and electro-pneumatic control systems, which are useful for testing PLC programs that interact with such systems. - LabVIEW:
While primarily a data acquisition and instrumentation software, LabVIEW can also simulate PLC behavior through its Real-Time Module.
Cloud-Based PLC Simulation
- COSIMIR Industrial (from KUKA): Provides cloud-based virtual commissioning and simulation for industrial automation systems, including PLCs.
These tools enable engineers and developers to validate PLC programs, simulate control strategies, troubleshoot potential issues, and test new configurations in a virtual environment before deploying them in industrial settings.
Each tool may vary regarding supported PLC brands, simulation features, and integration capabilities with other automation software.
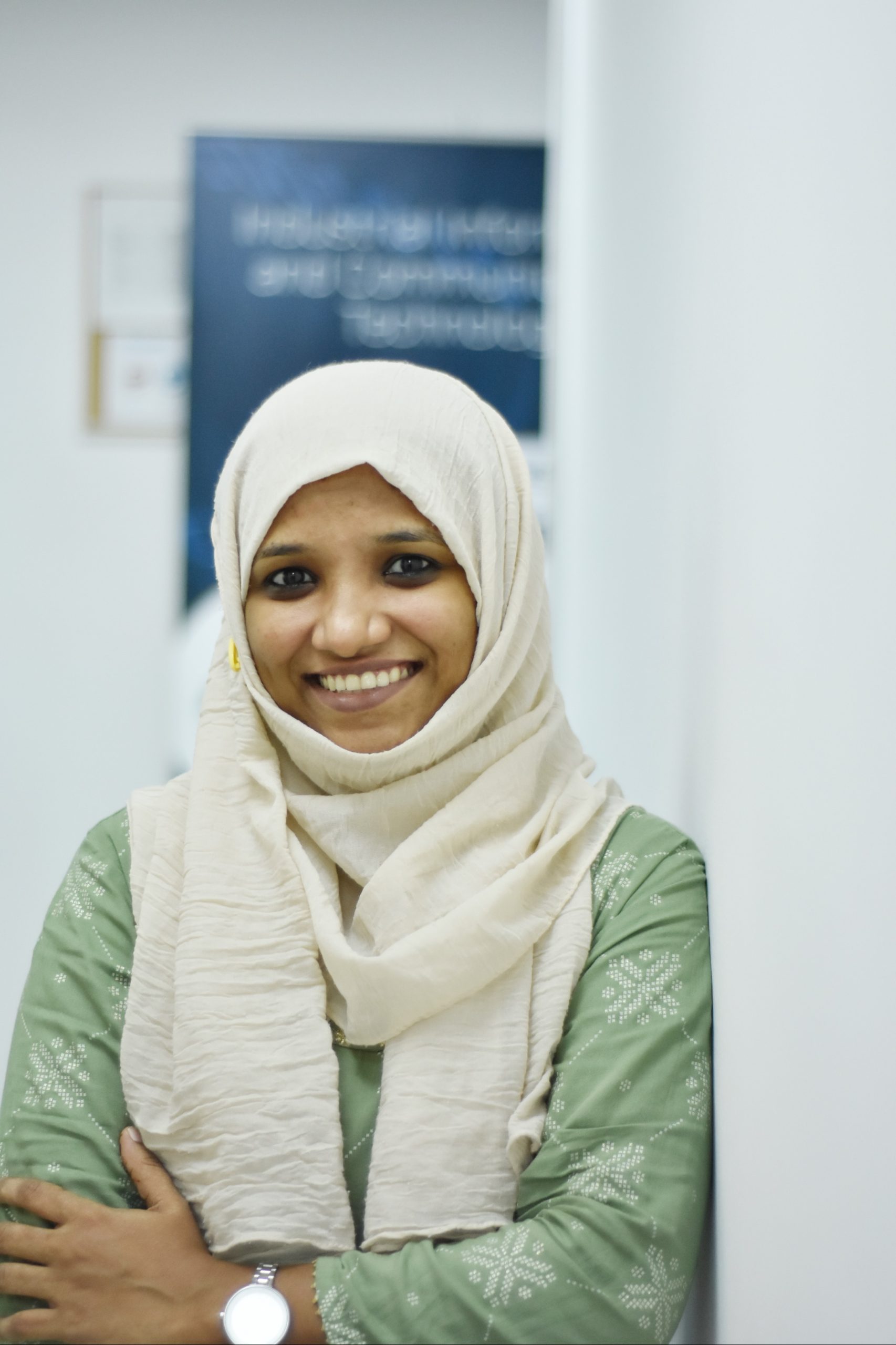
Fathima Sadina works as a Technical Associate at IIPD, where she dives into the world of Industrial Automation, focusing on PLC, SCADA, and VFD systems. With a keen passion for spreading know-how, she loves to craft engaging blog posts on a wide array of technical subjects.