In the dynamic and ever-evolving world of industrial automation, Programmable Logic Controllers (PLCs) stand as the foundational pillars, enabling precise control, seamless integration, and unparalleled efficiency across a wide range of industries. As the heart of modern manufacturing and process control systems, these versatile digital computers have become indispensable tools, driving innovation and transformation in sectors such as automotive, food and beverage, pharmaceuticals, and energy.
This comprehensive guide delves into the intricacies of Programmable Logic Controllers, exploring their core components, programming methodologies, diverse applications, and the remarkable benefits they bring to industrial automation. By understanding the capabilities of industrial PLCs, businesses can harness the power of these advanced technologies to streamline their operations, enhance product quality, and stay ahead in the competitive landscape.
What is a Programmable Logic Controller (PLC)?
A Programmable Logic Controller, or PLC, is a specialized digital computer used for automating electromechanical processes in industrial settings. Originally developed to replace relay logic systems, PLCs have evolved into sophisticated devices capable of handling complex control tasks, ensuring precision, efficiency, and flexibility.
Key Components of a PLC System
A typical PLC system consists of several essential components:
Central Processing Unit (CPU)
The brain of the PLC is responsible for executing control programs and coordinating communication between various modules.
Input Modules
These modules interface with sensors and switches, collecting data about the system’s inputs (e.g., temperature, pressure, position).
Output Modules
Connected to actuators such as motors, valves, and relays, output modules receive signals from the CPU and control the system’s outputs accordingly.
Memory
Stores the control program, system configurations, and data used by the PLC during operation.
Communication Interfaces
Facilitate communication between the PLC and external devices such as computers, Human-Machine Interfaces (HMIs), and other PLCs in a network.
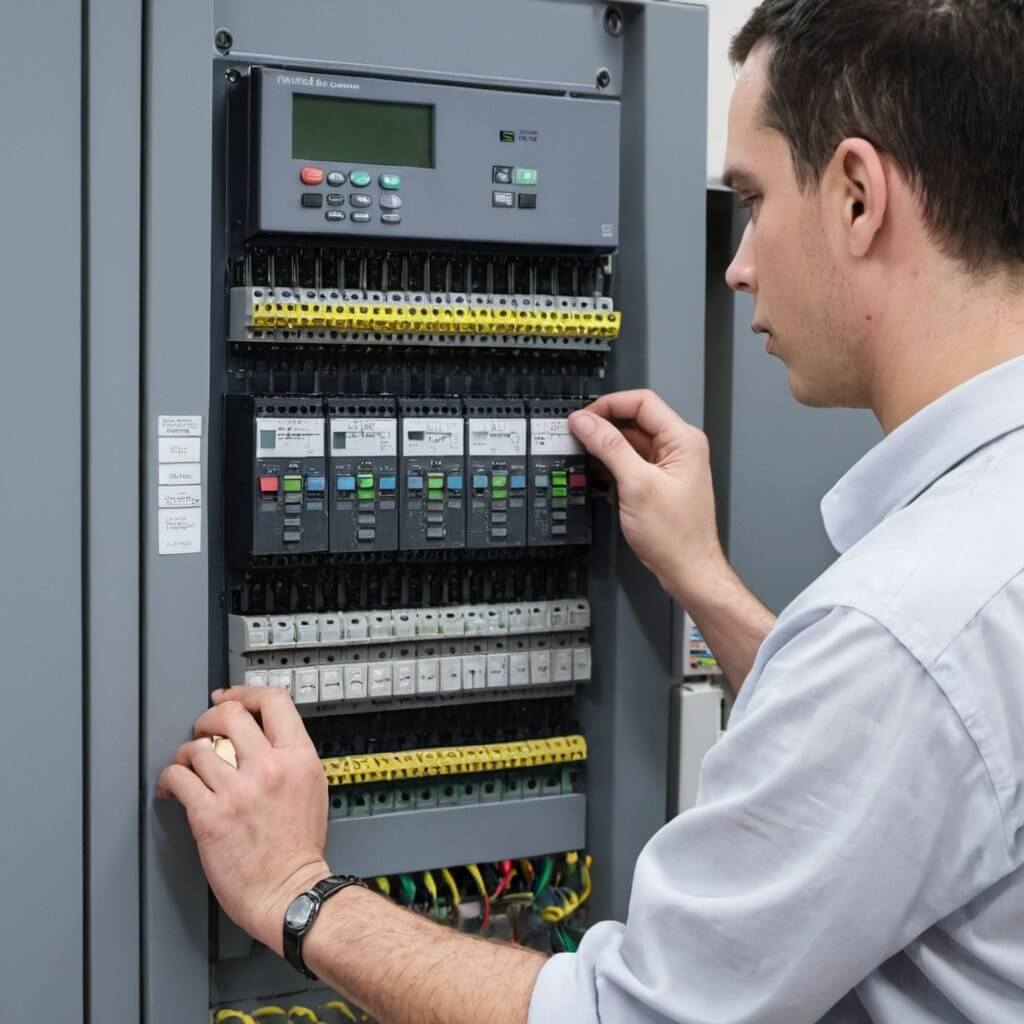
Programming PLCs
PLCs are programmed using specialized software tools, often based on ladder logic, a graphical programming language resembling electrical relay logic diagrams. As we discussed in our blog post, “What Programming Methods are Used in PLC?, other programming languages such as Function Block Diagrams (FBD) and Structured Text (ST) are also supported by many industrial PLCs, offering flexibility and versatility in programming approaches.
Applications of PLCs in Industrial Automation
PLCs find application in various industries, including manufacturing, automotive, food and beverage, pharmaceuticals, and energy. Some common applications include:
Automated Assembly Lines
PLCs control the sequence of operations on assembly lines, ensuring products are manufactured with precision and efficiency.
Process Control
PLCs regulate parameters such as temperature, pressure, and flow rates in industrial processes, maintaining optimal conditions and ensuring product quality.
Material Handling
PLCs control conveyor systems, robotic arms, and other equipment involved in material handling and logistics operations.
Building Automation
PLCs can also manage HVAC (Heating, Ventilation, and Air Conditioning) systems, lighting, and security systems in commercial and industrial buildings, optimizing energy usage and enhancing occupant comfort and safety.
Benefits of Adopting Programmable Logic Controllers
The integration of PLCs into industrial automation systems offers a range of benefits, including:
Flexibility
PLCs can be easily reprogrammed to accommodate changes in production requirements or process parameters.
Reliability
Built to withstand harsh industrial environments, PLCs offer high reliability and uptime, minimizing downtime and production losses.
Scalability
PLC systems can be expanded by adding additional modules or connecting multiple PLCs in a network, allowing for scalability as production needs grow.
Diagnostic Capabilities
PLCs provide real-time monitoring and diagnostic features, enabling quick identification and resolution of issues within the system.
Cost-Effectiveness
Despite their advanced capabilities, PLCs are cost-effective solutions for industrial automation compared to custom-built control systems.
Major Brands
Here’s a table with the major PLC brands and links to their official websites:
Brand | Official Website |
---|---|
Siemens | www.siemens.com |
Allen-Bradley (Rockwell Automation) | www.rockwellautomation.com |
Schneider Electric | www.schneider-electric.com |
Mitsubishi Electric | www.mitsubishielectric.com |
Omron | www.omron.com |
B&R Industrial Automation | www.br-automation.com |
GE Automation & Controls | www.ge.com |
Delta | www.deltaww.com |
Beckhoff Automation | www.beckhoff.com |
Bosch Rexroth | www.boschrexroth.com |
Phoenix Contact | www.phoenixcontact.com |
Conclusion
Programmable Logic Controllers play a vital role in industrial automation, offering precise control, flexibility, and reliability across a diverse range of applications.
As technology continues to advance, PLCs will remain indispensable tools for optimizing industrial processes and driving efficiency in manufacturing operations.
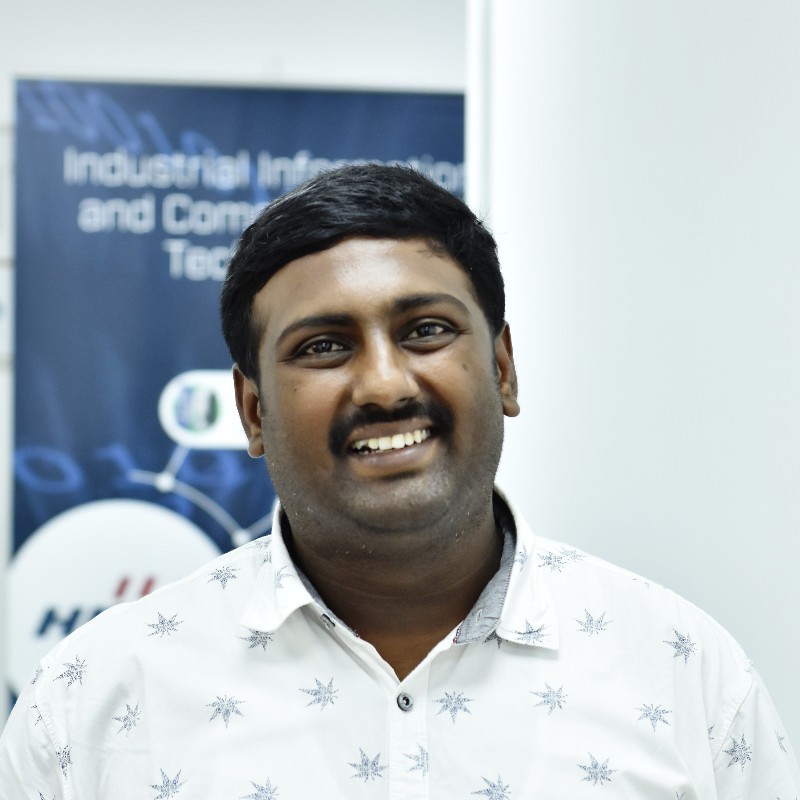
Senior Tech Manager at IIPD Global, weaving magic in Industrial, Building, and home Automation. KNX Tutor on a mission! Embracing Industry 4.0 and proudly shaping the tech landscape. Certified by CertNexus to ignite minds!