Integration of PLC (Programmable Logic Controller) systems, devices, and networks creates a unified control system. The primary objective of PLC integration is to enhance the efficacy and efficiency of industrial automation processes. PLCs are extensively used in manufacturing, process control, and building automation systems, and their integration can lead to increased productivity, decreased downtime, and improved product quality.
However, PLC integration can present obstacles such as compatibility issues, network security concerns, and system complexity. Therefore, cautious planning, implementation, and maintenance are essential for PLC integration to be successful.
What is PLC Integration and Why Does it Matter?
A Programmable Logic Controller (PLC) is the brains of your automation system. Integrating PLCs with other systems like HMI (Human Machine Interface), SCADA (Supervisory Control and Data Acquisition), and ERP (Enterprise Resource Planning) creates a unified control network. This unlocks a treasure trove of benefits:
- Real-Time Data Insights: Gain valuable insights into production processes by collecting real-time data from sensors and devices connected to the PLC. Analyze this data to identify inefficiencies, optimize workflows, and minimize waste.
- Remote Monitoring and Control: Empower operators to monitor and control systems from any location with internet connectivity. This flexibility enhances responsiveness to production changes and emergencies.
- Improved Efficiency and Productivity: Streamlined workflows, data-driven decision-making, and real-time problem identification lead to significant efficiency and productivity gains.
- Enhanced Product Quality: Monitor and control processes precisely with real-time data, leading to consistent and high-quality products.
PLC INTEGRATION METHODS
Hardwired Integration:
Hardwired integration is the process of physically connecting the PLC to other devices and systems via wires and cables. This approach is straightforward and trustworthy, and it can be utilized for straightforward applications that do not require a great deal of flexibility. However, inherent integration can be time-consuming and challenging to expand or modify.
Serial Communication:
Serial communication entails connecting the PLC to other devices and systems via a serial port. This method is adaptable and suitable for a wide variety of applications. Nevertheless, serial communication can be sluggish and susceptible to interference and other issues.
Ethernet Communication:
Ethernet communication involves connecting the PLC to other devices and systems via an Ethernet network. This method is efficient and trustworthy, and it can be applied to complex applications requiring a high degree of adaptability. Ethernet communication can be complex and may necessitate additional hardware and software.
OPC (Open Platform Communications) Integration:
OPC integration involves connecting the PLC to other devices and systems using an OPC server. This method is highly adaptable and applicable to a wide variety of situations. OPC integration can be complicated and may necessitate additional hardware and software.
Overcoming Integration Challenges
While PLC integration offers substantial benefits, challenges exist:
- Compatibility Issues: Ensure compatibility between PLCs, communication protocols, and other systems to avoid integration roadblocks.
- Network Security: Implement robust cybersecurity measures to protect your integrated system from vulnerabilities.
- System Complexity: Carefully plan and design your integrated system to manage complexity and ensure smooth operation.
Essential Considerations for Successful Integration
- Communication Protocols: Choose the right communication protocol (e.g., Ethernet/IP, Modbus) based on factors like data speed, network complexity, and device compatibility.
- Integration Methods: Explore various integration methods like hardwired connections, serial communication, Ethernet communication, and OPC (Open Platform Communications) to find the best fit for your needs.
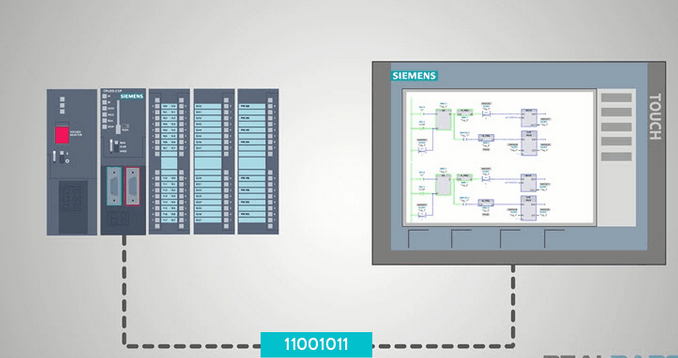
Integrating PLCs with Key Systems:
- HMI Integration: HMI provides a user-friendly interface for interacting with the PLC. Visualize data, adjust settings, and troubleshoot errors to optimize plant operations.
- SCADA Integration: SCADA allows centralized monitoring and control of the entire production process. Gain real-time insights, optimize production, and prevent faults. Key benefits include:
- Real-time monitoring for faster problem identification and resolution.
- Enhanced data collection for process optimization and productivity improvement.
- Historical data analysis to identify trends and improve processes.
- Remote access for increased flexibility and responsiveness.
- Improved visualization for better decision-making.
- ERP Integration: Synchronize data between the production floor and the office by integrating PLCs with ERP systems. This reduces errors, improves customer satisfaction, and allows for better planning and forecasting.
Conclusion: Reap the Rewards of PLC Integration
By strategically integrating PLCs with other systems, manufacturers can unlock a new level of efficiency, productivity, and quality. Careful planning, best practices, and innovative technologies are key to achieving a successful integrated automation system. Embrace PLC integration and gain a competitive edge in today’s dynamic manufacturing landscape.
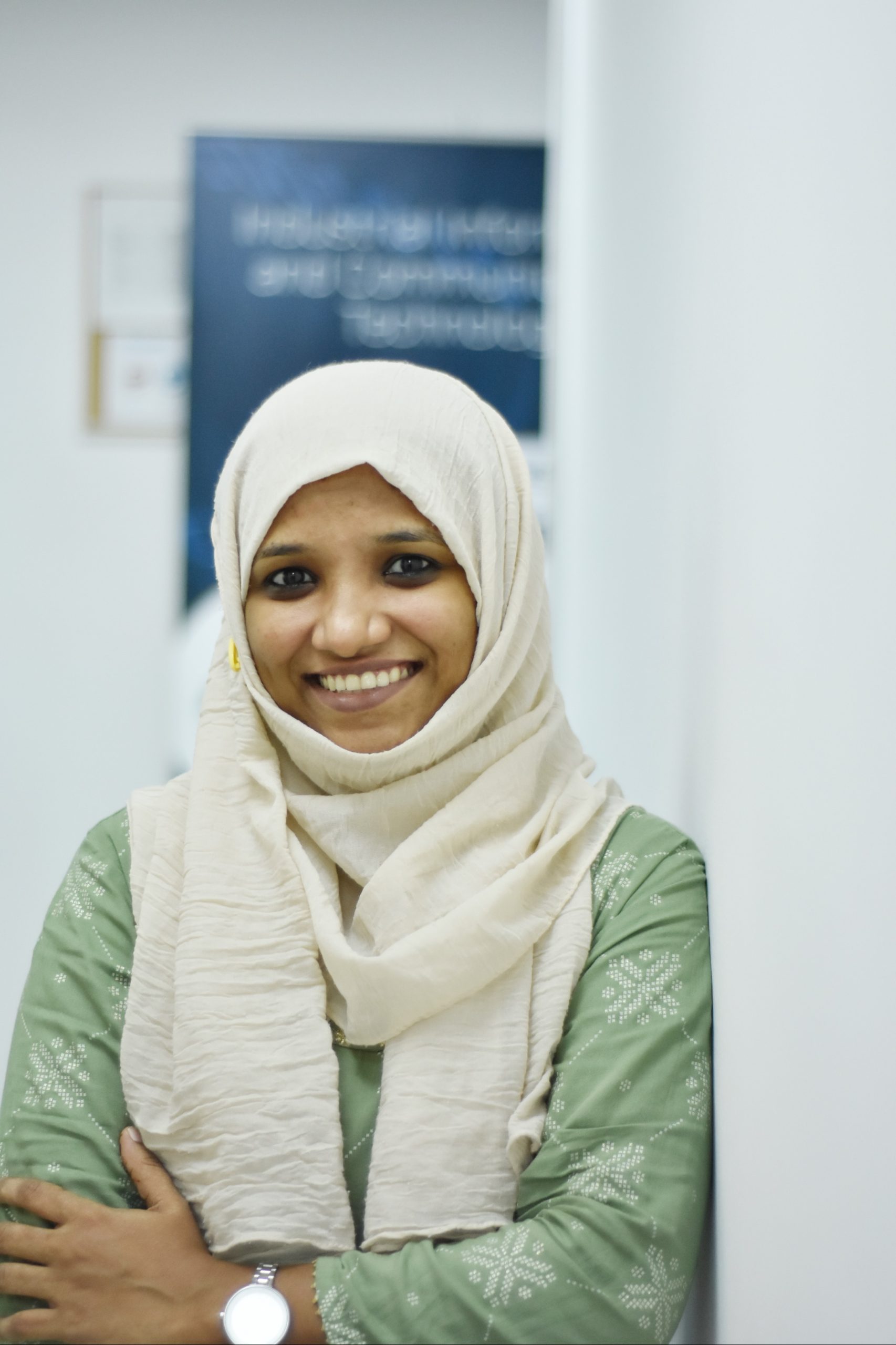
Fathima Sadina works as a Technical Associate at IIPD, where she dives into the world of Industrial Automation, focusing on PLC, SCADA, and VFD systems. With a keen passion for spreading know-how, she loves to craft engaging blog posts on a wide array of technical subjects.