In the intricate world of industrial automation, a sudden halt in Programmable Logic Controller (PLC) operations can bring production lines to a standstill, causing disruptions and losses. So in this article, we will discuss the reasons why a Programmable Logic Controller (PLC) goes into stop mode, and how to debug it, as debugging is essential to identify and rectify the underlying issues.
Reasons for PLC Going into Stop Mode:
In industrial automation, PLCs play a critical role in controlling machinery and processes. However, there are instances when a PLC unexpectedly enters stop mode, disrupting production. Let’s explore some common reasons behind this behavior:
Hardware Failures:
If any hardware error is detected in the PLC configuration such as malfunctioning input/output modules, internal wiring short circuits, or power supply issues, or a fault in the processor that can cause the PLC to enter stop mode to prevent further damage. It comes back to run mode when the hardware fault is resolved.
Error in Program Logic:
If there’s a software error in the PLC program, such as a syntax error, undefined variable, or incorrect instruction like when you in the program divide something by zero, the PLC might go into stop mode to prevent the execution of faulty code.
Communication Issues:
Problems in communication with external devices, such as input/output modules, sensors, or communication networks, can trigger a stop mode to avoid unreliable data processing.
Watchdog Timer Timeout:
PLCs often have a watchdog timer to monitor the program’s execution. If the program doesn’t progress within a specified time like any infinite instruction in the program that makes scan time longer, the watchdog timer might trigger a stop mode to prevent unpredictable behavior.
Downloading Program:
When you start to download any program to the PLC, it goes to stop mode.
Memory Mismatch:
A memory mismatch in a Programmable Logic Controller (PLC) occurs when there is a discrepancy between the expected and actual values stored in the PLC’s memory. This inconsistency can lead to unpredictable behavior, causing the PLC to go into stop mode.
Stop Switch & Digital input:
Some PLCs are equipped with a hardware switch that allows users to toggle between run and stop modes. This switch serves as a crucial safety measure, particularly in emergencies. When the switch is set to stop mode, the PLC is prevented from transitioning into run mode.
Additionally, in some PLC configurations, a digital input can be designated to function as a run-stop switch. In this scenario, the PLC will only operate in run mode when the assigned input is in a high state, ensuring controlled and intentional activation of the system.
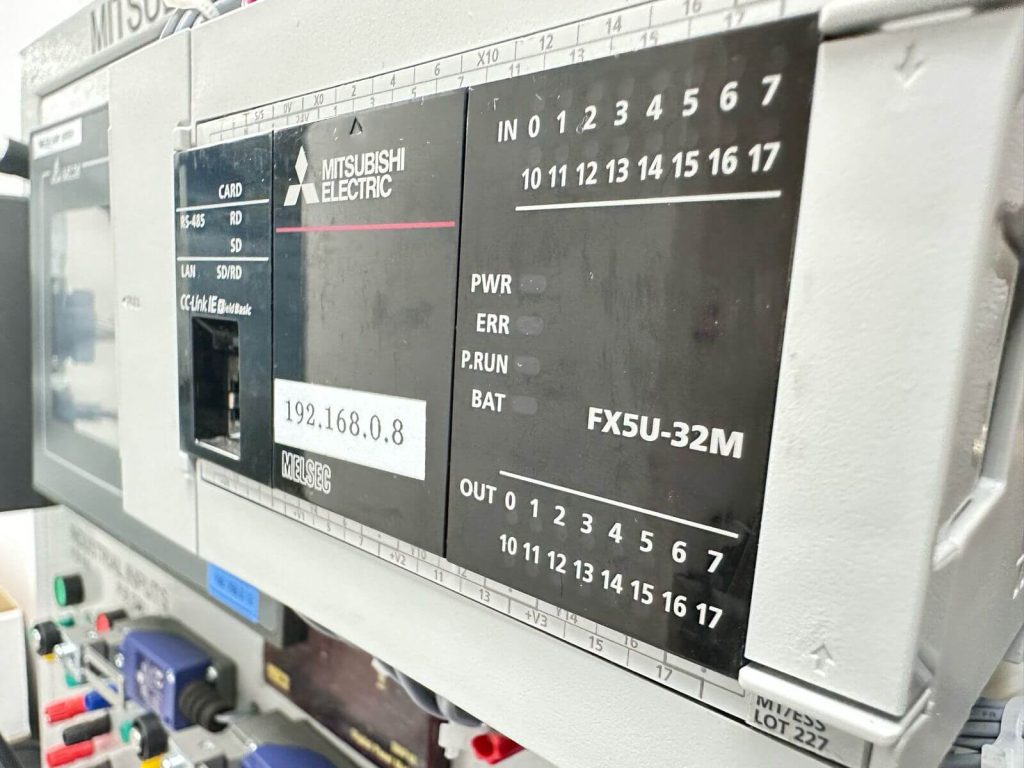
Debugging Steps:
We’ll explore various methods and techniques used in debugging, including code inspection, debugging tools, unit testing, integration testing, system testing, monitoring, and logging. So, let’s roll up our sleeves and uncover the secrets of effective debugging!
Check Program Logic:
Review the PLC program for any syntax errors, undefined variables, or incorrect instructions. Use the programming environment (e.g., CODESYS) to identify and correct programming mistakes.
Examine Error Messages:
PLCs usually provide error messages or diagnostic information. Check the PLC’s display, diagnostic LEDs, or error logs for any messages that can indicate the cause of the stop mode.
Review Communication Setup:
Verify the communication settings with external devices. Check cables, connections, and network configurations to ensure proper communication. Look for any error codes related to communication issues.
Inspect Hardware Components:
Physically inspect the PLC hardware components, including input/output modules, power supplies, and the central processing unit (CPU). Look for any signs of damage, loose connections, or malfunctioning components.
Check Power Supply:
Ensure that the power supply to the PLC is stable and within the specified voltage range. Fluctuations or interruptions in power can lead to erratic behavior and trigger a stop mode.
Review Watchdog Timer Settings:
If the PLC has a watchdog timer, review its settings. Ensure that the timer duration aligns with the expected program execution time. Adjust the settings if necessary to prevent false triggering.
Use Online Monitoring:
Utilize the online monitoring features of the programming environment. This allows you to observe the execution of the program in real-time, identify which part of the code is causing the issue, and check variable values.
Logging and Diagnostics:
Enable PLC logging and diagnostics to capture information about the program’s execution. Analyze these logs to identify patterns, error codes, or recurring issues that may lead to stop mode.
Update Firmware/Software:
Ensure that the PLC firmware and programming software are up to date. Manufacturers often release updates to address bugs or improve system stability.
Consult Documentation:
Refer to the PLC’s documentation, manuals, and troubleshooting guides provided by the manufacturer. These resources can offer insights into common issues and solutions.
By systematically going through these debugging steps, you can identify the root cause of the PLC entering stop mode and take corrective actions to ensure the system operates as intended.
Conclusion:
In the fast-paced world of industrial automation, the sudden halt of Programmable Logic Controller (PLC) operations can result in significant disruptions and losses for production lines. This article has delved into the various reasons behind a PLC entering stop mode, ranging from hardware failures to programming errors and communication issues. Understanding these triggers is essential for maintaining operational efficiency and minimizing downtime.
Moreover, we’ve outlined a comprehensive debugging process, encompassing code inspection, error message examination, hardware inspection, and utilization of monitoring tools. These steps, coupled with thorough documentation review and firmware/software updates, constitute a systematic approach to identifying and rectifying PLC issues.
For individuals seeking to deepen their understanding of PLC operations and troubleshooting techniques, specialized PLC training courses such as those offered by IIPD Global can provide invaluable insights and skills. With a solid grasp of PLC functionality and debugging methodologies, professionals can effectively ensure the smooth functioning of industrial automation systems, thereby optimizing productivity and minimizing downtime.
In essence, by proactively addressing PLC stoppage issues through diligent debugging practices and continuous learning, industries can maintain their competitive edge and enhance operational reliability in the dynamic landscape of industrial automation.
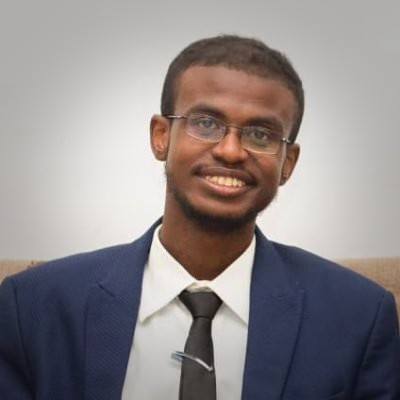
Passionate about empowering engineers in Industrial Automation, Instrumentation, IIOT, and beyond. Dedicated to sharing insights, expertise, and fostering innovation in the dynamic world of technology.