Industrial automation plays a pivotal role in shaping the modern manufacturing landscape by automating repetitive and complex tasks. This improves efficiency, contributes to higher product quality, and reduces operating costs. The integration of automation technologies has become a fundamental aspect of staying competitive in today’s fast-paced industrial world.
In the ever-evolving landscape of industrial automation, Programmable Logic Controllers (PLCs) play a pivotal role in ensuring precision and efficiency in manufacturing processes. This article delves into the reasons behind the widespread use of PLCs.
Importance of PLC in Industrial Automation:
At the heart of industrial automation, Programmable Logic Controllers, commonly known as PLCs, are electronic devices designed to control and automate industrial processes with high precision. PLCs have evolved into sophisticated controllers capable of handling a wide range of tasks. These devices are programmable, allowing for the customization of control logic to suit specific industrial needs.
PLCs are the backbone of industrial automation, functioning as the central control hub for machines and processes. They receive input from sensors, process information, and send output commands to actuators. PLCs can be programmed to execute complex sequences of tasks, making them versatile tools across various industries.
The significance of PLCs lies in their ability to provide real-time control over various industrial processes. PLCs are employed in manufacturing units, assembly lines, and even power plants to regulate processes with precision, resulting in increased productivity and reduced downtime. The reliability and flexibility of PLCs make them indispensable in industries where automation is key.
Brief History:
Before the advent of PLCs, industrial automation relied heavily on complex relay-based control systems. These systems used electromechanical relays to control various aspects of industrial machinery.
Traditional control systems based on Relay were complex, bulky, and challenging to modify. PLCs revolutionized this scenario by offering a compact, programmable alternative. The shift from traditional control systems to PLCs marked a paradigmatic leap in the world of industrial automation.
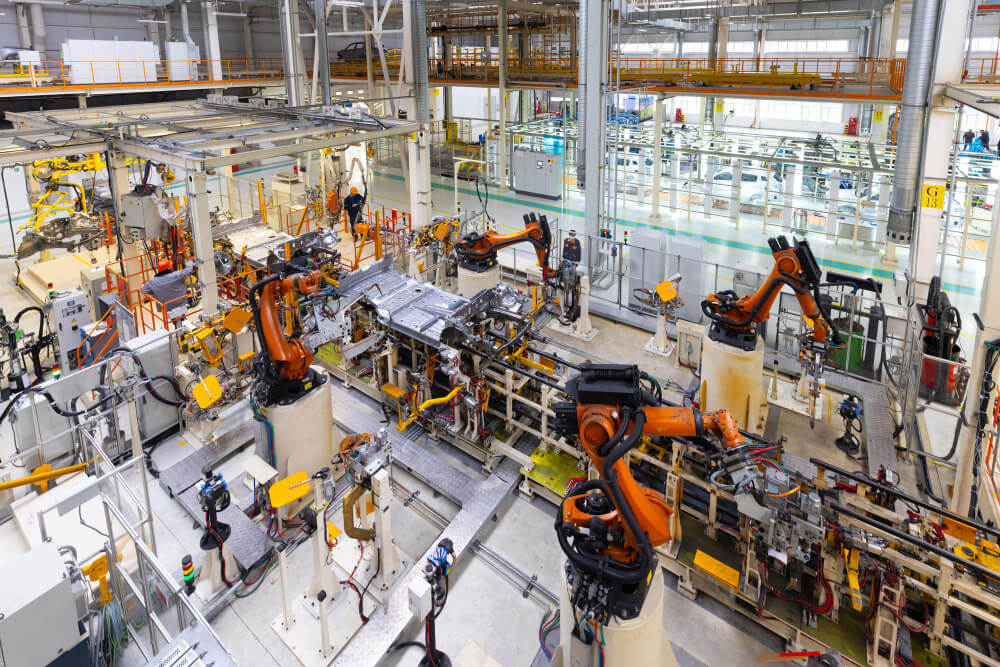
Why do We Need PLC in industrial Automation?
We have multiple reasons to use PLCs such as: improving the efficiency and reliability of industrial processes, reducing the cost and complexity of wiring and hardware, and enabling easy reconfiguration and modification of the control logic.
PLCs are specialized computers that can monitor and regulate machines and manufacturing processes in various environments with automation technology.
They can perform discrete and continuous functions, such as timing, counting, calculating, comparing, and processing various analog and digital signals. PLCs are also designed to operate reliably under harsh industrial conditions, such as extreme temperatures, humidity, and vibration.
Flexibility and Adaptability:
One of the primary reasons for the widespread use of PLCs in automation is their unparalleled flexibility and adaptability. Unlike traditional control systems that require extensive rewiring for modifications, PLCs allow engineers to alter control logic through programming. This flexibility ensures that manufacturing processes can be easily adapted to accommodate changes in product specifications or production requirements.
Real-time Control:
PLCs excel in providing real-time control over industrial processes, a crucial requirement in modern manufacturing. Whether it’s regulating the speed of a conveyor belt, monitoring temperature variations in a furnace, or coordinating complex assembly line tasks, PLCs execute commands with precision and immediacy. This real-time responsiveness is vital for maintaining the integrity of production timelines and ensuring optimal efficiency.
Customization for Specific Industrial Needs:
The ability to customize control logic makes PLCs indispensable for addressing specific industrial needs. Different industries have distinct requirements, and PLCs can be programmed to cater to these specific demands. From automotive manufacturing to food processing, the adaptability of PLCs ensures that they seamlessly integrate into diverse industrial settings.
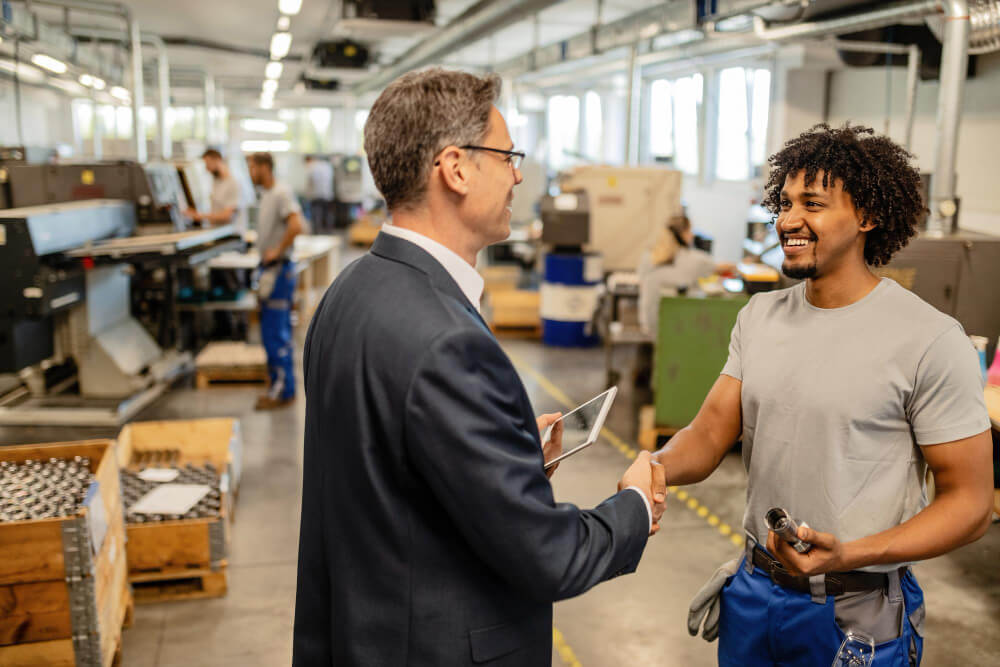
Reliability and Durability:
In the harsh environments of industrial facilities, reliability is non-negotiable. PLCs are renowned for their robustness and durability, making them well-suited for the demanding conditions of manufacturing plants. Their design incorporates features like resistance to dust, moisture, and temperature extremes, ensuring uninterrupted operation even in challenging settings.
Improved Diagnostics and Troubleshooting:
PLCs simplify the diagnostic and troubleshooting processes in industrial automation. With detailed feedback on the status of input and output signals, engineers can quickly identify issues and rectify them. This capability reduces downtime and enhances overall system reliability, a crucial factor for industries where every minute of operation translates to productivity and profit.
Cost-effectiveness:
While the initial investment in PLCs might seem substantial, their long-term cost-effectiveness is undeniable. The adaptability and ease of reprogramming mean that changes in production processes can be implemented without significant additional costs. Additionally, the reduction in downtime and improved efficiency contribute to cost savings over the operational life of the PLC system.
Integration with Other Automation Technologies:
PLCs seamlessly integrate with other automation technologies, such as SCADA systems, to create comprehensive control solutions. The interoperability of PLCs allows for a unified approach to industrial automation, where different components work in tandem to optimize processes. This integration capability positions PLCs as a central component in the broader ecosystem of automation technologies.
Ultimately, the use of Programmable Logic Controllers in automation is not merely a technological choice but a strategic imperative for modern industries. The unparalleled flexibility, real-time control capabilities, customization options, and integration capabilities position PLCs as the driving force behind the optimization of industrial processes. As industries continue to evolve and embrace the era of smart manufacturing, PLCs will remain at the forefront, ensuring efficiency, precision, and adaptability in the ever-changing landscape of industrial automation.
FAQ:
Is PLC SCADA in demand?
Yes, PLC and SCADA skills are in demand in various industries, especially those involved in industrial automation.
Is PLC SCADA easy to learn?
Learning PLC and SCADA can vary in difficulty depending on individual aptitude and prior knowledge. However, with proper training and dedication, they are generally considered accessible.
Which is best, PLC or SCADA?
A direct comparison between PLC (Programmable Logic Controller) and SCADA (Supervisory Control and Data Acquisition) is not feasible as each serves different purposes in the industrial automation system. PLC is responsible for real-time control and executing programmed tasks, while SCADA operates at a higher level, managing and monitoring these processes.
Can we connect PLC to SCADA?
Yes, PLCs can be connected to SCADA systems for comprehensive control and monitoring of industrial processes. This integration enhances overall system visibility and management. There are different technologies such as OPC.
Which language is best for PLC?
The best programming language for PLC depends on the specific application and industry and the choice of programming language depends on factors such as the programmer’s background, the nature of the problem, and the control system’s structure. Common languages include Ladder Logic Diagram (LD), structured text (ST), and Function Block Diagram (FBD) you can find more here What programming methods are used in PLC?
Is PLC a good career?
Yes, pursuing a career in Programmable Logic Controllers (PLC) can be a promising choice, especially in the context of the ongoing industrial revolution. PLCs play a crucial role in modern industrial automation, facilitating efficient control and monitoring of processes across various industries.
Who can study SCADA?
SCADA can be studied by individuals with backgrounds in engineering, computer science, or related fields. Those interested in supervisory control and automation systems can pursue SCADA education.
How many days it will take to learn PLC SCADA?
The duration varies based on individual aptitude and prior knowledge. With focused learning, one can gain proficiency in PLC and SCADA within a few months.
What is HMI in SCADA?
HMI (Human-Machine Interface) in SCADA refers to the graphical interface that allows operators to interact with the control system. It provides real-time data visualization and control options.
What is an HMI in PLC?
A Human Machine Interface (HMI) is a user interface that allows interaction between an operator and a machine, system, or process in industrial automation. It displays real-time data, controls equipment, and provides a platform for monitoring and managing operations. HMIs incorporate visual elements like graphics, buttons, and indicators, enabling users to monitor processes, input commands, and receive feedback, enhancing efficiency and control in industrial settings.
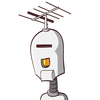
Phasellus at auctor nibh. Morbi feugiat finibus nulla, et semper ipsum sodales a. Fusce at lacus vestibulum, luctus sapien quis, dictum erat.