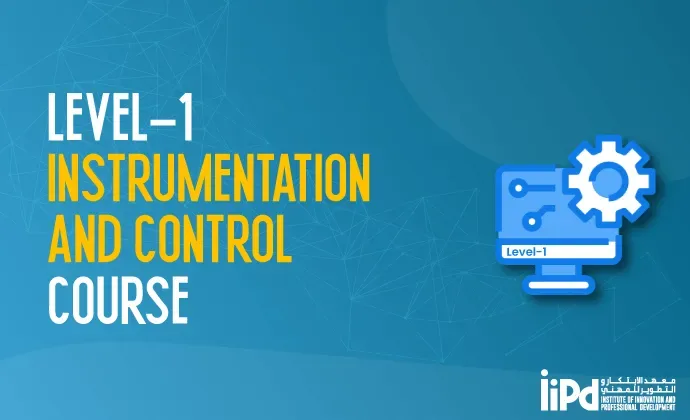
Course Details
The course has been designed to familiarize Electricians and engineers with the fundamentals involved in Control and Instrumentation. The course will cover temperature, pressure, and flow transducers. The students will be introduced to Single loop PID Controllers and PLC PID control and how signals are connected, and how the controllers are configured.
The students will be shown how and use plant actuators controlled from the controllers, which will lead to an introduction to PID configuration.
Introduction to Open and closed loop systems
- What is control and instrumentation? Simple terms will be introduced: setpoints, PVs, CVs, actuators, disturbances, etc.
- Understanding the difference between open and closed loop systems. and the terms velocity lag and time constant.
- Brief explanation of how temperature is measured? Explanation of thermocouples, bi-metallic, Pyros and Rtd’s, wiring, testing and excepted readings. The students will all have practical exercises to work through. Also, the installation and positioning of the temperature transducers will be discussed and practiced.
- What are transmitters, and when are they used? The students will wire a thermocouple and RTD to a transmitter to produce a 4 to 20ma or 0-10v signal. Highlight why 4-20ma is used.
- Introduction to calibration of feedback devices: why it is needed and the process of how temperature devices are calibrated.
- Introduction to controllers: The students will be shown how dedicated signal loop controllers can be used or PLC
- Introduction to a temperature closed loop control.
- Pressure transducer construction.
- The students will test and understand the 4-20ma loop for a Pressure transmitter..
- Introduction to a basic pressure closed loop system.
- Introduction to PID terms: Proportional Band, Reset and Rate, and calculations for the PID terms.
- Understanding flow measurement and transmitters.
- Introduction to a basic flow closed loop system.
- Understanding Level measurement and transmitters.
- Introduction to a level closed loop system.
- Insight into to forward and reverse acting control loops.
- Description of the terms velocity time lag.
- The students, through a set of exercises, will change the PID terms and note responses.
- Common faults that could occur in a closed loop system and the consequences.
- Introduction to the Pipe and Instrument diagrams..
- Explain the terms 'transfer lag' and 'time constant' and interpret time constants.
Field Instruments
- When using PLC's Identify Digital I/O, Analogue I/O, Counter cards.
- Describe the signal expected at the input and output of each type of card.
- Describe how to measure the level of an analogue input for a 0-10v and 4-20mA signal for a 25%, 50% and 75% input, including the corresponding number expected in the controller.
- Explain how to follow a digital input from a switch through to the code in a PLC.
- Demonstrate the use of I/O schedules to locate inputs and outputs for field instruments.
Calibration
- Describe the principles and reasons for calibration.
- Describe the significance of span zero and the interaction of adjustments.
- Describe how the calibration of measuring instruments relates to the latest Quality Assurance Standard.
- Describe the acceptable tolerances and the cumulative nature of these tolerances.
- Describe the use of test samples.
- Describe the use of tables and calibration data for input of test signals.
- Apply the procedure and methodology of calibration.
Temperature
- Distinguish between non-electrical, electrical, and radiation methods of measurement of temperature.
- Describe the application and operation of given types of instrument,s e.g. bi-metal element, liquid in glass, liquid in metal, resistive element, thermo-couple, pyrometer, etc.
- Describe the range, limitations, and typical process applications of given methods of measurement.
- Test and calibration of an RTD, PYROs and Thermocouples and using transmitters.
- The students will then be set a task to convert a temperature to a PLC PID controller, which will involve writing software using transmitters and scaling signals and tuning the PID.
- Fault finding on a temperature closed loop control.
This course is a great starting point for electricians and engineers looking to build real-world skills in control and instrumentation. From understanding sensors and transmitters to configuring controllers and tuning PIDs, you'll get hands-on experience with the systems used in today's plants. By the end, you'll know how to set up, test, and troubleshoot basic closed loop systems with confidence—skills you can apply right away on the job.