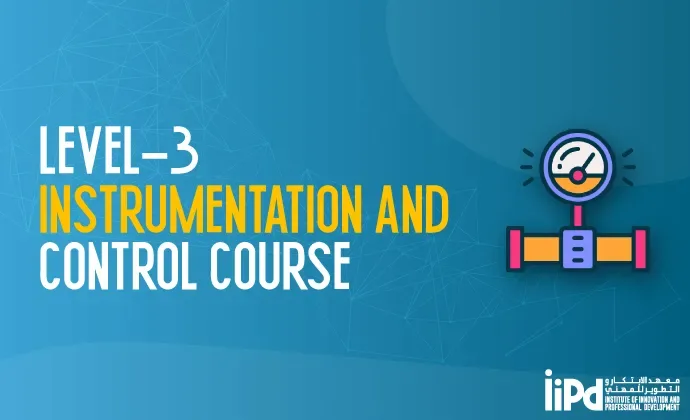
Course Details
The course has been designed to familiarise Electricians and engineers with the fundamentals involved in Control and Instrumentation. The course will cover temperature, pressure, and flow transducers. The students will be introduced to Single loop PID Controllers and PLC PID control and how signals are connected, and how the controllers are configured.
Prequisites:
- Level 1 Instrumentation Course Certificate
- Level 2 Instrumentation Course Certificate
The students will be shown how and use plant actuators controlled from the controllers, which will lead to an introduction to PID configuration.
E31 Level Element 1
- Explain the types and operation of level-measuring elements.
- Distinguish between measurement of levels of liquids and solids..
- Describe the operating principle behind each given method e.g. float gauges, manometers, diaphragm, capacitance, nucleonic, load cell, strain gauges, etc.. and their applications.
- The range and limitations as well as the applications for these units, shall be explained.
E31 Level Element 2
- Explain the operation, testing and calibration of given instruments.
- The students will work on a rig controlling level with a pressure level measurement and Ultrasonic measurement.
- This will include calibration, test and safety Isolation of the instrument.
E31 Level Element 3
- Explain the function, operation, and setting of given controllers.
- Using the PID function in inverter drives to control flow
- A further explanation of Control valves and the procedure for calibration using an I/P.
- Using the PID function in inverter drives to control flow
- Understand the operation of control cylinders and valves and the calibration techniques.
E31 Level Element 4
- Commission, adjust, test, and fault find on given instruments, controllers, and control loops.
- Overhaul, test, and calibrate given instruments.
- Explanation of the Overhaul, test and calibrate of a level instrument.
- Commission and tune given control systems.
E44 Control and PID Element 1.
- Explain the use of ‘two step’ control and ‘overlap’.
- Define ‘on/off control and give examples of its application.
- Explain the effect of ‘dead time’ on two-step control.
- Describe the main disadvantage of two-step control.
- Define ‘proportional action’.
- Explain the proportional band.
- Calculate proportional bands from given data.
- Define ‘gain’.
- Define the term ‘off-set’.
- Explain how off-set’ relates to load changes.
- E44 Control and PID Element 3.
- Explain the use of ‘Integral control action’ and ‘integral action time’.
- Define ‘integral action’.
- Draw graphs illustrating proportional and integral action.
- Define the term ‘integral action time’.
- Explain ‘re-set’ in terms of integral action time.
- Calculate integral action time and proportional band from given data.
Element 4.
- Explain the use of ‘derivative control action’ and ‘derivative action time’.
- Define ‘derivative action.
- Describe the type of processes, that make use of derivative action control and how it is applied.
- Explain the effect of ‘derivative action time.
- Calculates derivative action’ from given data.
- Draw graphs showing ‘derivative action.
This course offers a solid, hands-on introduction to level measurement and PID control for electricians and engineers. From understanding how level sensors work to configuring PLC-based control systems and tuning loops, you'll gain real-world experience with the tools and techniques used in modern process plants. It's a practical way to build your skills and confidence in control and instrumentation.